A Standard Operating Procedure (SOP), also known as Standard Operating Procedure, is an essential tool for employees to perform their tasks in an efficient and structured manner.
An SOP provides clear, step-by-step instructions on how to complete a task successfully. By following an SOP, employees know exactly what steps are needed, eliminating variation and miscommunication in the process. This not only contributes to consistency, but also makes it easier to quickly train new employees and continuously implement improvements.
Although standardization can sometimes be seen as limiting, it actually brings peace and structure. It helps employees focus on the actual work, without having to reinvent the wheel every time. In this article, we will discuss what an SOP is and how you can use it to optimize processes within your organization. With an SOP, you get the most out of your team and increase the efficiency of your business operations.
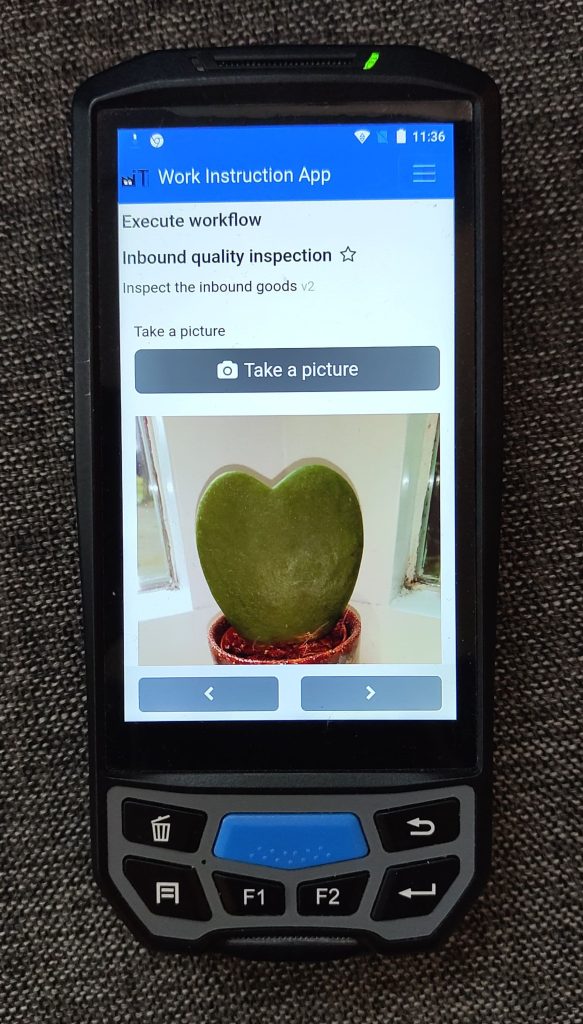
Create sound Standard Operating Procedures
Step 1: Make an overview of the processes you want to standardize.
The best approach is to have teams, with or without their managers, draw up a list of processes that may be suitable for SOPs. The management team can then assess these processes and prioritize them. Keep in mind that not all processes need or can be standardized.
Expert tip: In this first phase, it is tempting to want to create an SOP for every process. However, this is not the intention. Focus on processes that do not need to be continually adjusted in the future.
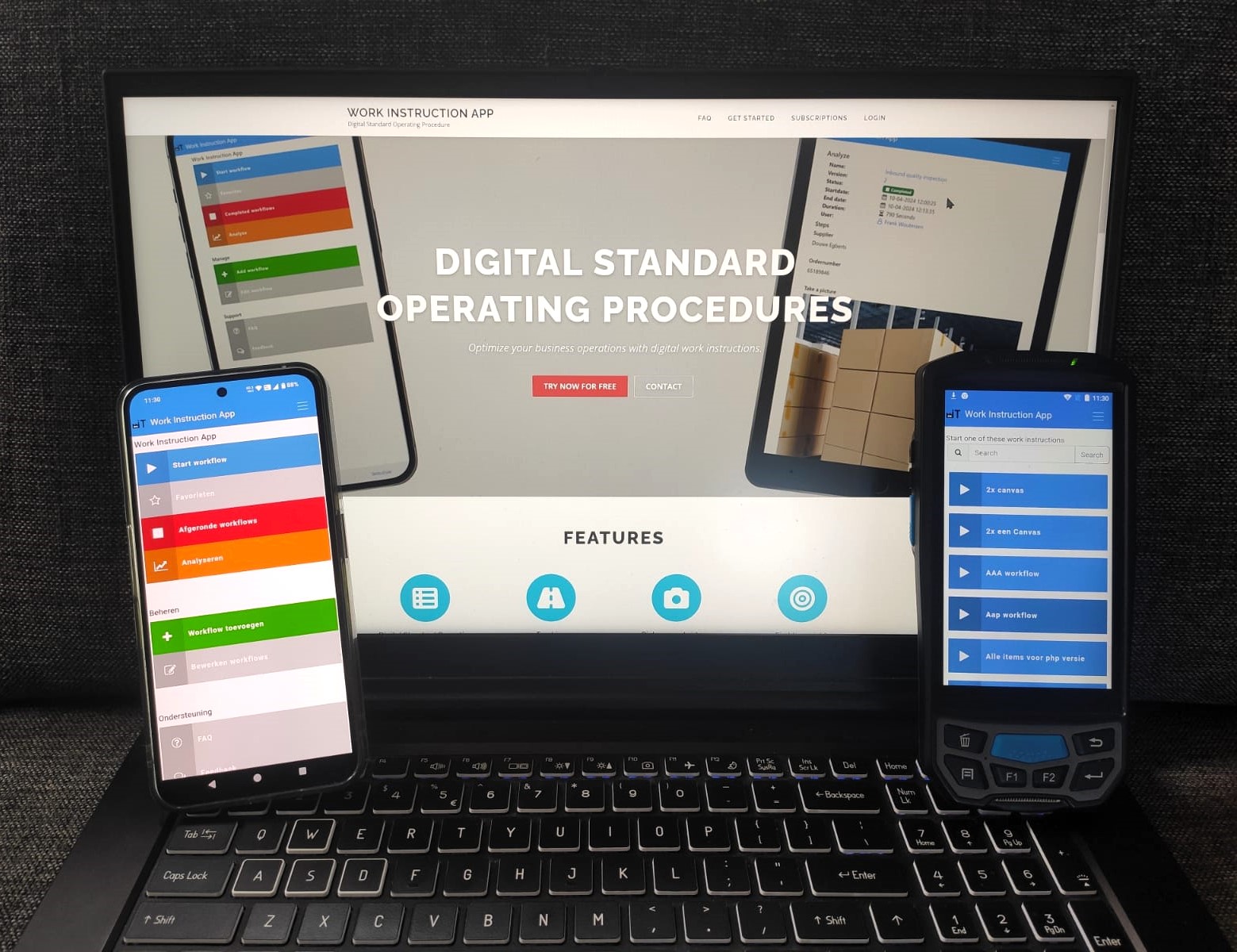
Step 2: Develop a plan for developing and managing the SOPs
Create a clear and consistent format/template:
Once you have a list of processes you want to document, it’s time to start creating your SOPs. This starts with developing a standard format that each SOP follows. Think about how you want the information to be presented: will you use step-by-step instructions, diagrams, flowcharts, or a combination of these? Always keep your audience in mind. Next, create a template so that all SOPs have the same structure and look and feel, making them easier to use and understand.
Create an effective review process:
Next, create a process for reviewing and approving your SOPs. It’s crucial to have a structured approach to ensure that each SOP is reviewed and approved before it’s put into use. Designate one person who is responsible for approving, managing, and quality control your SOPs.
Make them digitally accessible:
Make your SOPs easily available to your employees. Use the Work Instruction App so that all your employees have access to the latest SOPs.
Step 3: Collect the necessary information for the SOP
Voordat je begint met het verzamelen van informatie, is het belangrijk om een plan op te stellen voor hoe je dit gaat aanpakken.
Identificeer de procesexperts: Een van de beste manieren om relevante informatie te verkrijgen, is door in gesprek te gaan met de experts die dagelijks met het proces werken. Plan interviews met hen in om waardevolle input te verzamelen voor het opstellen van de SOP.
Controleer of er al bestaande informatie is: Kijk ook of er al bestaande SOP’s zijn binnen bepaalde afdelingen of bij andere organisaties die je als basis kunt gebruiken. Zo voorkom je dubbel werk en kun je voortbouwen op bestaande kennis.
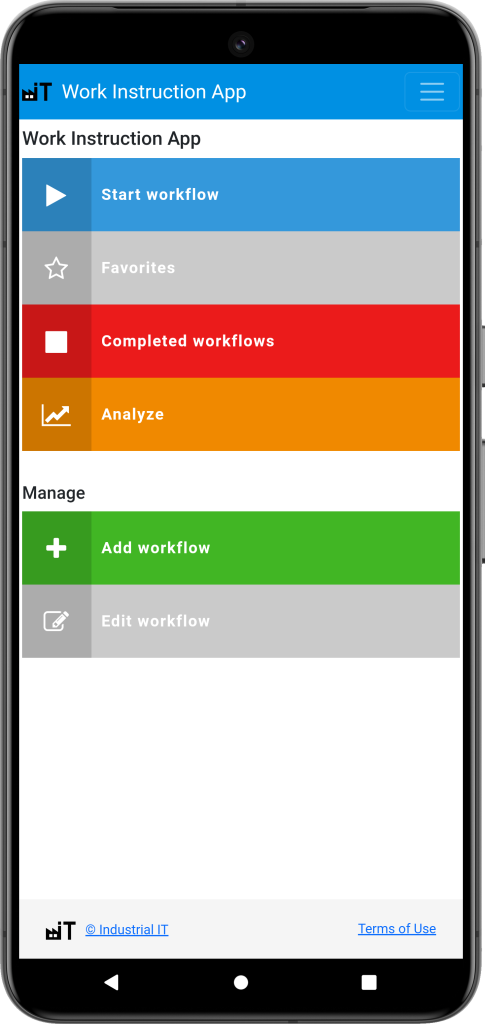
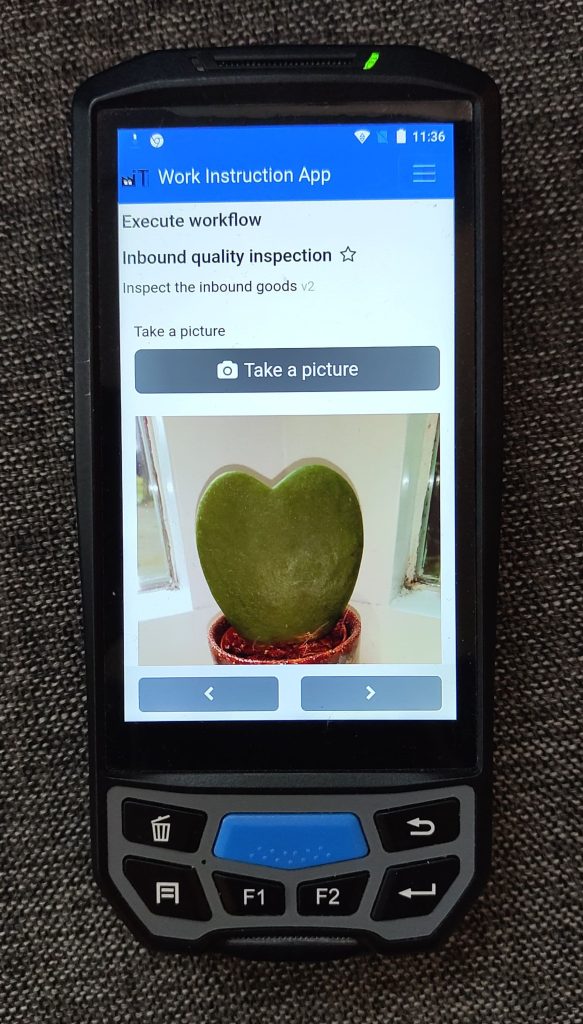
Step 4: Write the SOP, discuss it and publish it
After completing step 3, you can begin drafting the first version of your Standard Operating Procedure (SOP). Fill in the template with the information you gathered during the interviews with the process experts. It is important to have the developed template reviewed by the experts to ensure accuracy. Most organizations follow these steps:
- Have the SOP reviewed by the process expert.
- Obtain input from management.
- Ensure that the quality requirements for each process are clearly defined.
Then publish the SOP(s) to the users within the organization.
Step 5: Ensure your SOPs are updated and maintained regularly
Now that you have an SOP in place and made it available, it is important to develop rules for continuous improvement. This process of continuous improvement can also be standardized and documented – a separate SOP for managing and updating existing SOPs. This is crucial, since you have invested a lot of time and effort in creating quality SOPs. To prevent them from becoming outdated due to changes in processes, it is essential to keep them up to date. Create a system where employees can submit suggestions for improvements or updates, and assign an administrator to maintain the SOPs.
Pro tip: Keep it simple. Organizations often tend to standardize too many processes. The number and level of detail of SOPs should be tailored to the target audience and the maturity of the organization.
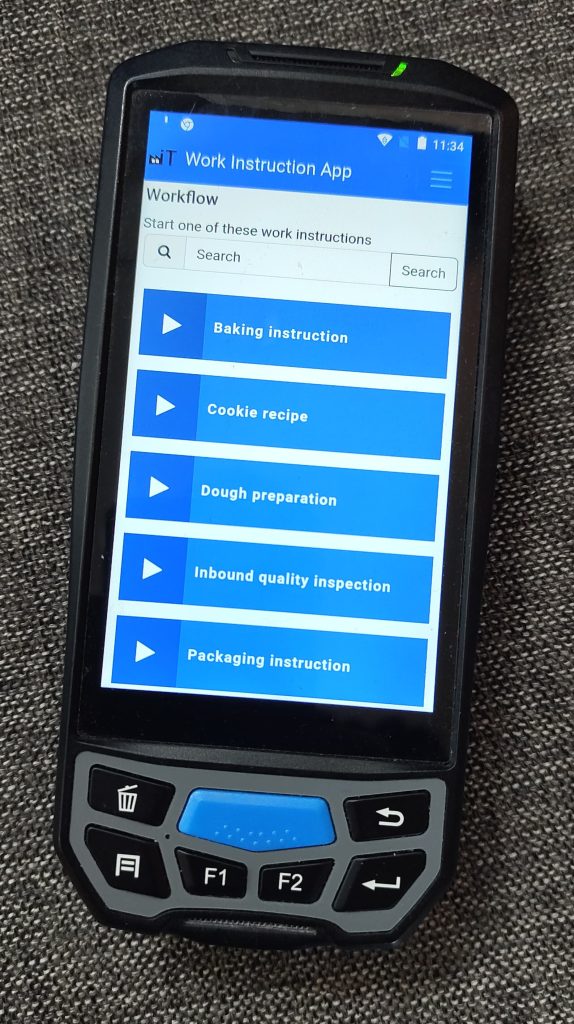